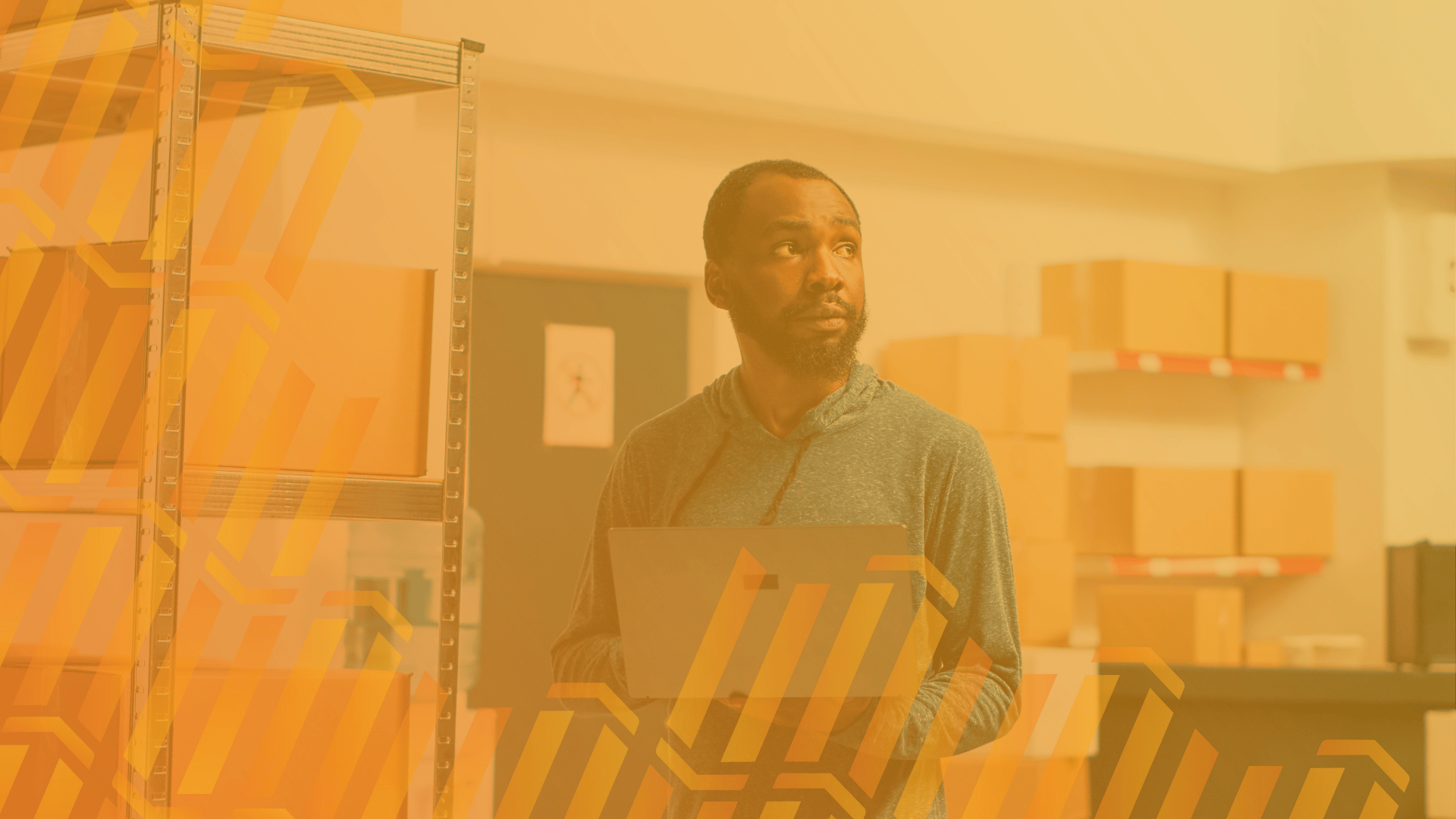
Keeping a stockroom organised can be a logistical nightmare.
Whether you own a small family-run business or manage a larger corporation, issues with stock control and inventory management can drastically impact your business.
So what’s the best way to organise your stockroom?
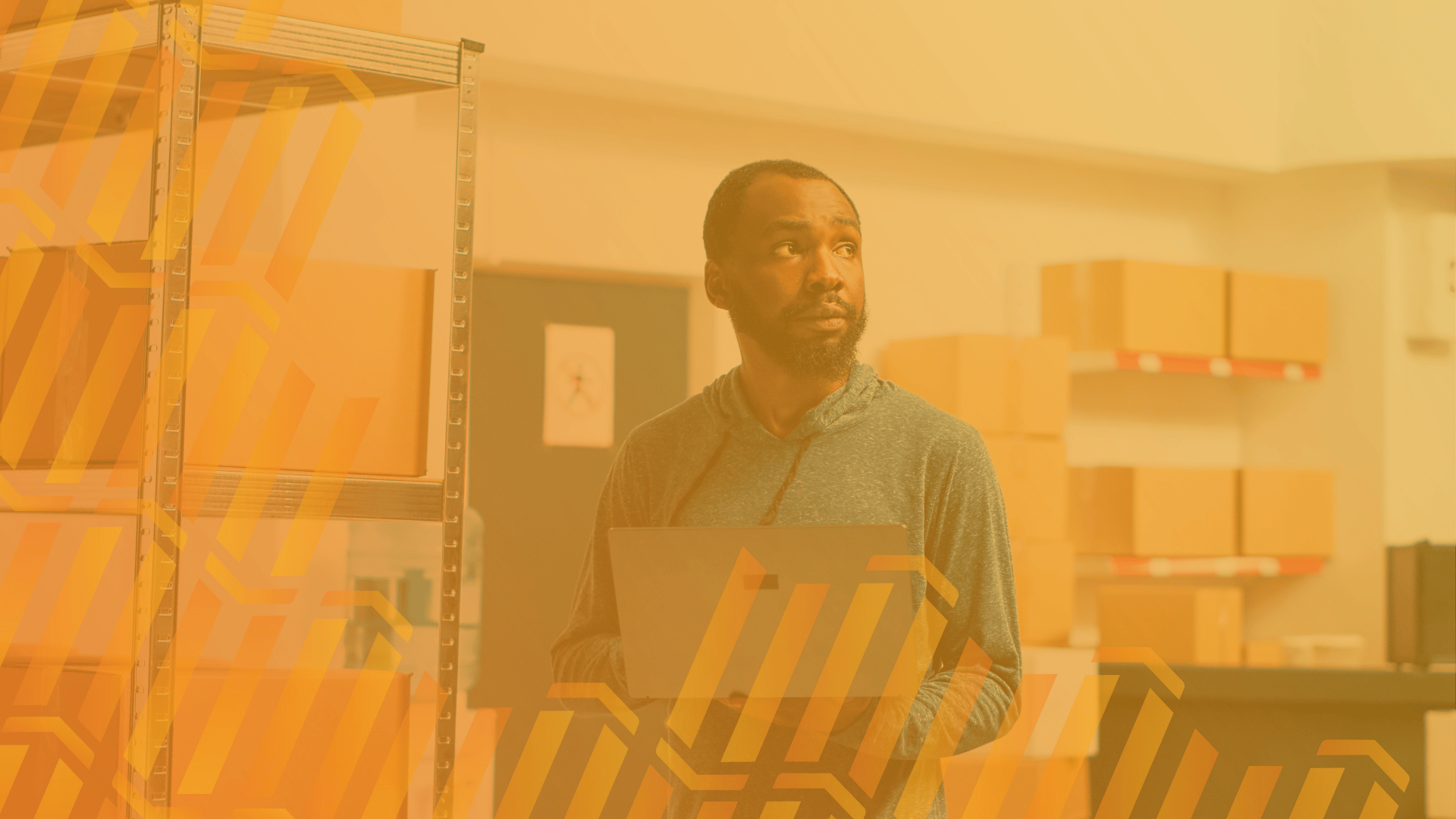
Why not have a listen?
Why does stockroom management matter?
Mismanagement can turn stockrooms into dysfunctional nightmares. The longer you leave it, the worse the mess gets, and the more money you stand to lose.
However, the cost of a disorganised stockroom isn’t just money:
“During the busy season, there’s no margin for error. If you run out of a product you need… it can disrupt a number of customers’ schedules and shake their trust when you make a mistake like that.”
Ryan Michel, Defense Pest Control
The knock-on effect of disorganisation can mean losing your customers’ trust, that staff get frustrated, and you lose clarity about your own cash flow.
To help, we’ve put together expert advice so you can create a stockroom that works. With these tips, you can take steps to better organise your stockroom and reap the benefits of effective inventory management.
Many of the tips shared come from the retail industry. These businesses tend to be the most forward-thinking in how they manage their stockrooms, but their insights translate perfectly for HVAC, plumbing and electrical businesses like yours.
Let’s dive into the solutions below:
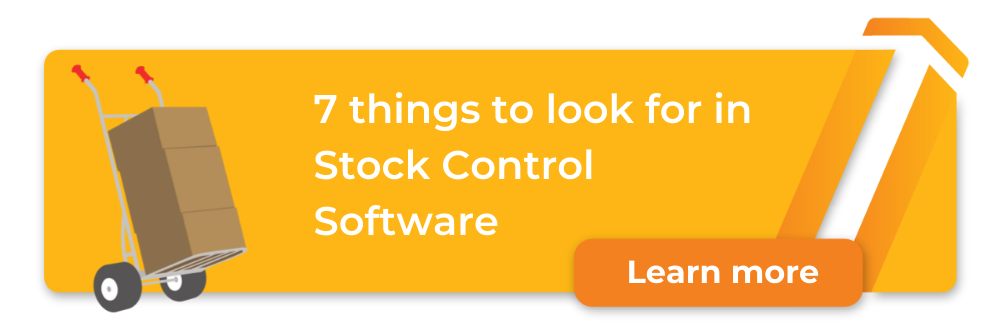
How should I organise my stockroom?
Here’s a quick overview of the top tips for how to organise your stockroom:
With these steps, you can begin to craft the perfect stockroom for your service, maintenance, or installation business.
1. Figure out what storage solutions suit your business
It’s about more than just shelves!
You’ll need shelving for your stockroom, sure, but there’s more to storage than a few good metal racks.
We recommend sitting down with your team to figure out what solutions could benefit you all. Getting feedback will inform how you eventually decide to layout your stockroom.
As far as choosing which organisational solutions could help you most, you’ll find many affordable storage solutions from businesses like Shopfitting Warehouse, The Shelving Shop, and BiGDUG.
Whether it’s your first location or an upgraded stockroom, it’s important to ask questions like:
- Do you want wall-mounted or freestanding racking?
- What kinds of storage bins should you store your stock in?
- Do you need accessories like corner protectors?
As we’ve suggested, by talking with colleagues, suppliers, and fellow business owners, you can get more ideas about how best to improve your own storage rooms and other solutions.
Ryan Michel, at Defense Pest Control spoke about a solution they found in this exact way:
“Right now we have metal shelving units that we picked up from another pest control company that was buying new ones.”
You never know what’s out there until you start looking and inspiration can come from anywhere.
2. Purchase shelving that maximises your vertical space
As we said: shelves still matter. So have you considered going up, not just out?
Even if you feel you’ll have enough space by using short shelving, you should consider getting the tallest shelves that you can fit into your space.
This is a sensible move that can help you plan for the future and help you to make the most of your space.
It can be easy for smaller businesses to neglect the space they have. You don’t want to scramble or retrofit impractical solutions as this can be expensive and time-consuming.
Replacing short storage shelves with taller ones later is a waste of money, so take advantage of all the space you have when reorganising your stockroom.
3. Label your shelves and bins clearly
Your engineers need to know where stock is stored, which items are available on each shelf, and in which storage bins, too. This is why clear labelling matters.
If you use a digital stock control system, you may rely on barcode scanning to help here. Whether it’s a device like the image you see here or an app to use on a smartphone, scanning stock will help you digitally label and better document stock with ease.
This process of labelling, tracking, sorting, and finding the right items in your stockroom will become much easier, with this tool. It also means that stock and inventory levels can be checked remotely, without anyone having to physically enter the room.
Imagine the time and effort that can be saved!
As a suggested step, Ryan Michel uses a label maker to identify which shelves hold which materials, and also leaves the original labelling on the products themselves. This helps his engineers and technicians find things faster. It’s also much easier to go through inventory when you’re working your way down a list.
As far as creating labels goes, Clearly Inventory, has a great article on how to make good labels for inventory locations. It’s a simple but effective solution that can keep your stockroom organised so that each and every service, maintenance job, and more, can run more efficiently.
4. Make popular stock easily accessible
It’s key to have the most popular stock in the easiest-to-reach places.
This way, employees can grab what they need and get back out on the floor in moments, rather than minutes.
It’s the same for field service businesses!
Figure out what parts are needed for your most common repairs and installations, and make sure they’re easily accessible for your busy engineers. This way, they can grab what they need, log it quickly, and be on their way.
5. Ensure your shelves fit inside your stockroom
Do you want to maximise storage space in your stockroom?
This example of how you can adapt your stockroom shelves to match the inventory they carry:
“Imagine your stockroom contains a shelving unit with five shelves, each with a height of 40cm for a total height of 200cm.
In other areas you are storing 20cm high boxes, which works perfectly, but in this case you are hoping to store 30cm high boxes.
If you decide to keep the same shelving configuration, you will be losing 10cm for every shelf, resulting in only 80 per cent space utilisation.
A simple reconfiguration to 30cm shelf heights would increase your utilisation to 90 per cent.”
Small Business
The lesson here? Don’t pile bins haphazardly onto your stockroom shelves.
Instead, adjust the shelving as needed to make the best use of your space, and you’ll be able to fit more stock and make it more easily accessible.
6. Place heavy items low and lighter items high
Simple as it sounds, practical advice helps as much as logistical tips, too.
Physically, it’s helpful to keep the heavy stock items on or close to the ground, and lighter stock higher up on shelves. This will keep the racking from toppling over and make it easier for your engineers to get the stock they need, significantly decreasing the likelihood of hurting themselves.
It’s as easy as putting the light stuff high, and the heavy items low down. Obvious as it seems, you’d be surprised just how few people do this well, not to mention safely.
7. Do regular clean-ups of your stockroom
It’s important to regularly clean out your stockroom and a good ol’ fashioned tidy-up is easier if you’re already following the steps outlined above.
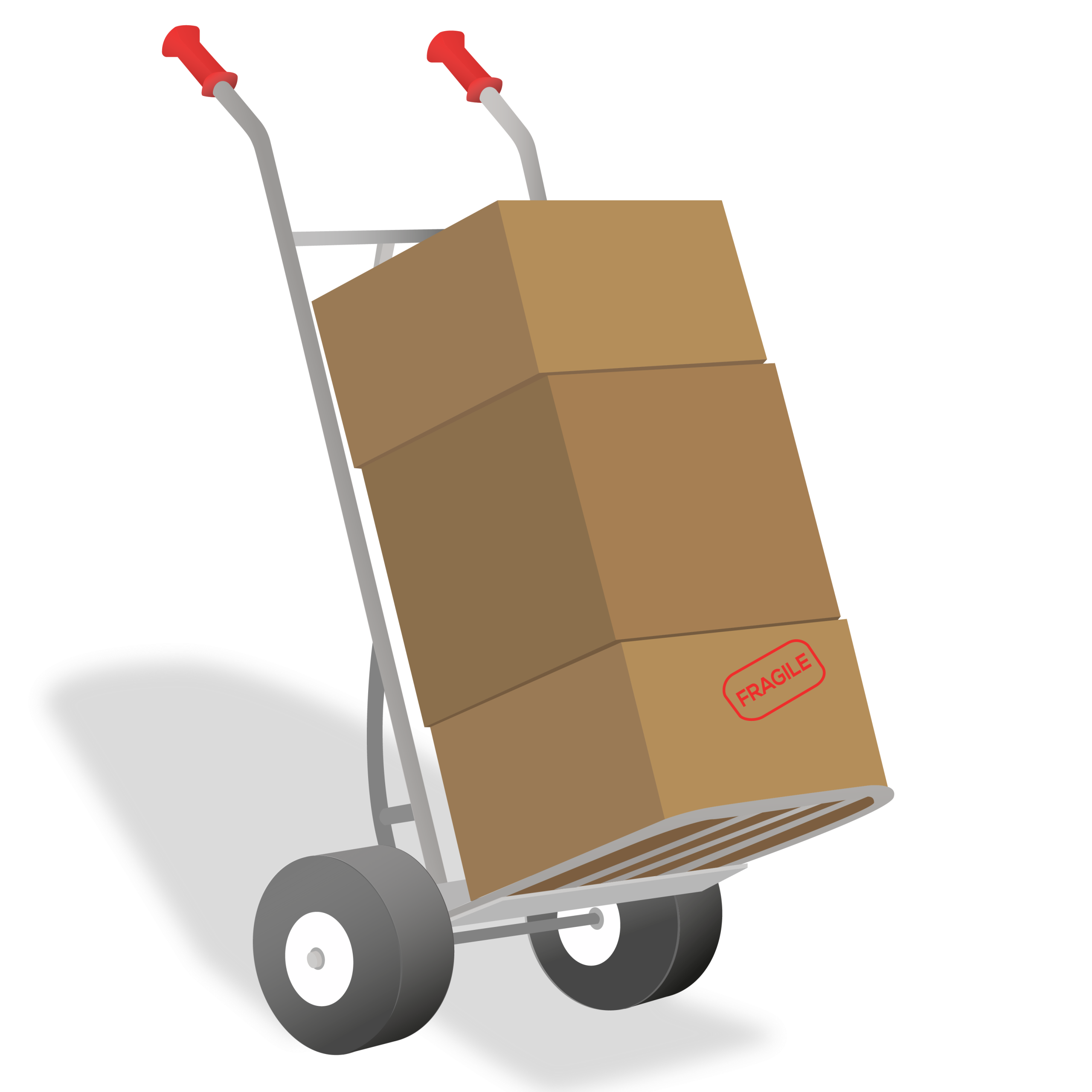
Besides, you never know what old or ‘missing’ stock you’ll find during a clean-up, and you can also clear away outdated parts (even selling them on if they’re better used elsewhere) to help make space for the stock you do want.
If your stockroom is big enough, you could even think about adding nice aesthetic touches, like plants, or even painting a wall an attractive colour. It’s a simple thing, but how you fill a space can make a huge difference in how you interact with it. If a room is made to look nice, people are far more likely to want to keep it that way.
For instance, if your employer branding uses particular colours, why not paint a wall in that colour? Certain colours can even be subconsciously energising and the subtle effects can be a pleasant surprise!
Think about lighting, too. Walking into a bright stockroom is energising and will help your team find what they need, much more than if they walk into a dark and dusty, mess.
Taking regular inventory presents a good opportunity to check through your stockroom.
8. Train your engineers to manage the stockroom space
Digital stock and inventory control offers a fantastic solution to managing your stockroom far better than any paper-based system could. Though it’s true, to use it well, engineers need training.
No matter what solution you use for organising your stock, be sure to train your engineers in how to use it—and in using it consistently—otherwise, your perfectly laid-out stockroom will soon become a disorganised mess.
The easier your stockroom system is to use, the more your engineers will comply and the more efficiently they can work. To help create an effective stockroom training program for engineers, consider:
“Getting a new set of eyes to look at a current situation and ask why you do things this way.”
Life Cycle Engineering
Similarly to talking to your own team about what works for them, bringing in a fresh perspective could help highlight solutions you didn’t know you needed.
In addition, when hiring a new engineer who hasn’t used your stockroom before, don’t be afraid to hear their suggestions. If they’re an experienced engineer, they may have tips and tricks from other businesses you’d find useful.
Feedback can help you build a functional stockroom that works.
How well is your stockroom organised?
By following the advice above, you should soon have a stockroom that works perfectly for your business.
Of course, stock management will require diligent attention to keep things organised but if you’re looking for a solution to assist you explore what Commusoft’s field service management software can do for you!
Learn all about the benefits of Commusoft’s Stock Control software.
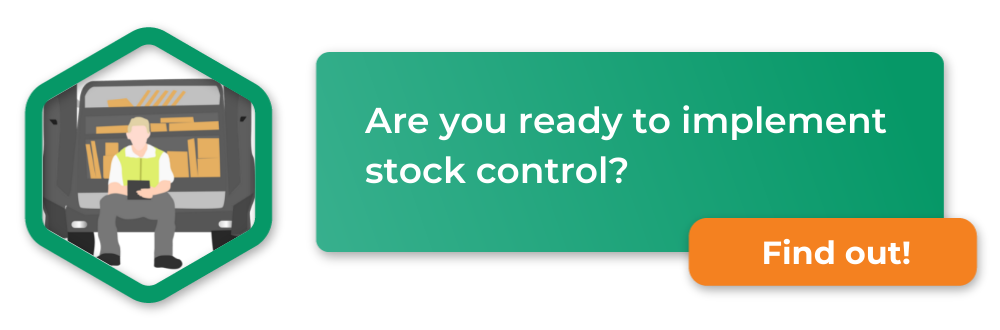